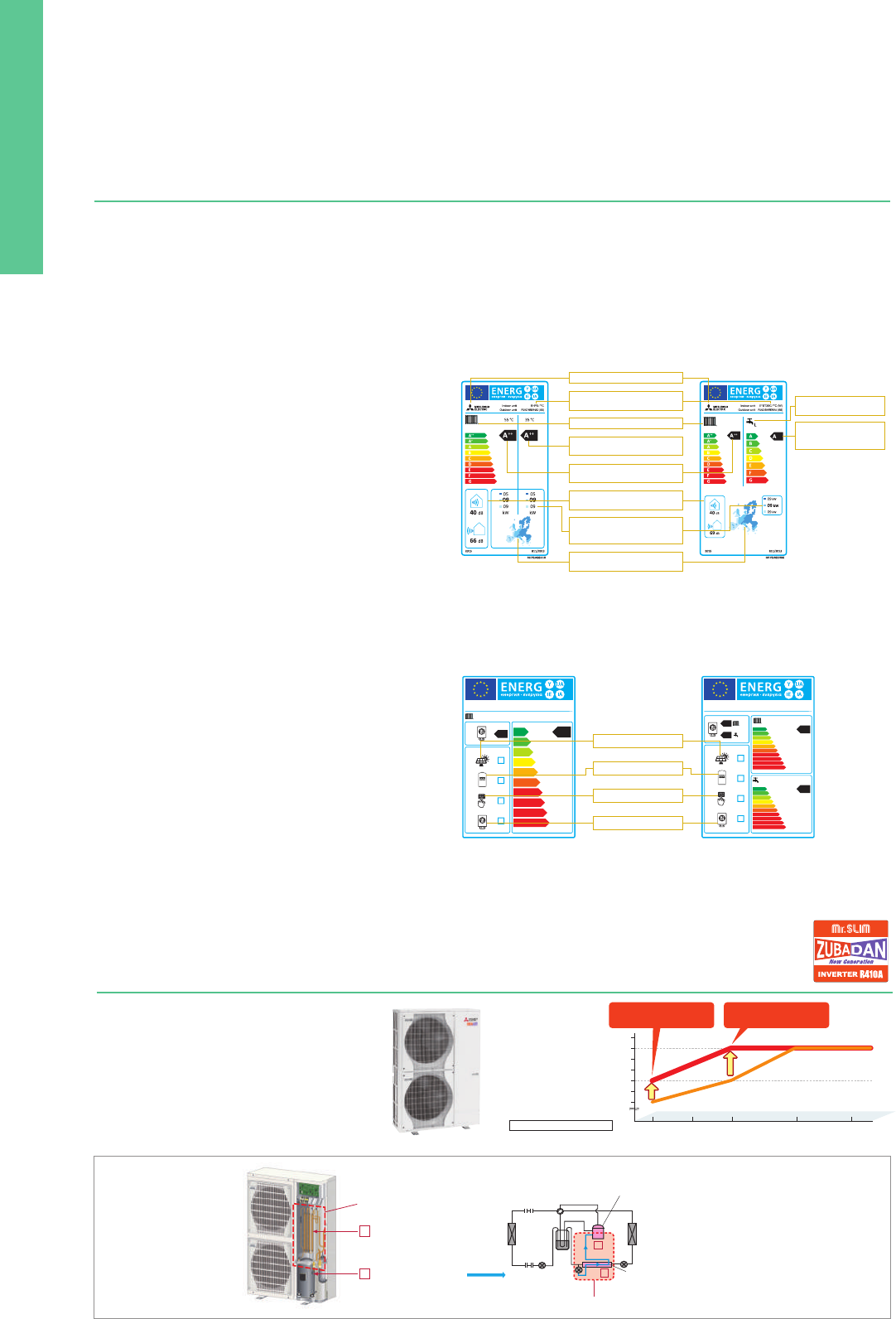
145
What is the ErP Directive?
ZUBADAN New Generation (Split type)
Reliable performance in low-temperature outdoor air
ZUBADAN New Generation provides powerful
heating in cold regions where most heat pumps
cannot perform very well. Its rated heating capacity
is maintained even in outdoor temperatures as low
as –15°C, even when flow temperature needs to
be higher. That means it can be trusted to provide
comfortable heating during severe winter months.
The Ecodesign Directive for Energy-related Products (ErP Directive) established a framework to set mandatory standards for ErPs sold in the Euro-
pean Union (EU). The ErP Directive introduces new energy efficiency ratings across various product categories. It affects how products such as
computers, vacuum cleaners, boilers and even windows are classified in terms of environmental performance. Labelling regulations that apply to
our ATW heat pumps come into effect as of September 26, 2015.
Under directive 2009/125/EC, ATW heat pumps of up to
70kW are required to show their heating efficiency on the
energy label. The purpose of the energy label is to inform
customers about the energy efficiency of a heating unit.
The efficiency for space heating is ranked from A
++
to G.
In the case of domestic hot water, it is from A to G.
A package label is also required if the ECODAN heat pump
is installed with a controller and/or a solar system or addi-
tional heater. All ECODAN units* are already rated as A
++
for heating at both 55°C and 35°C and A for domestic hot
water, which are the highest efficiency ranks.
*Except for our ATA/ATW hybrid system Mr. SLIM+
New energy label and measurements
New eco-design directive
Designed for Optimal Heating
Heat pump space heater label
These labels are delivered with all ECODAN outdoor units.
Combination heater label
Manufacturer
Symbol for
domestic hot water
DHW efficiency during
medium-temperature
operation
Outdoor and indoor unit
model name
Symbol for space heating
Heating efficiency in
low-flow temperature operation
Heating efficiency in
medium-flow temperature operation
Indoor and outdoor unit
operating sound power level values
Rated heat output
(
kW
)
under average,
colder and warmer conditions
European temperature
climate map
This label is for individual heating units, such as an ECODAN heat pump. Typically, the space
heater label is used for ECODAN systems with a hydro box, and the combination heater label
is used for ECODAN systems with a cylinder unit.
Product label
A heating system can use several energy-related prod-
ucts, such as a controller or solar thermal system. There-
fore, a label showing the efficiency of the total heating
system is required. The category range is defined from
A
+++
to G.
Creating the package label is the responsibility of the in-
stallers and distributors. A useful tool on the Mitsubishi
Electric website is available to easily create the labels for
ECODAN products and controllers.
erp.mitsubishielectric.eu/erp/options
What is the package label?
This label is for heating systems that use several energy-related products, such as a controller
or a solar thermal system.
Package label
Customised package labels including ECODAN heat pumps and FTC5 controller
can be created on the Mitsubishi Electric website.
Package space heater label Package combination heater label
+
+
+
+
A
+++
A
++
A
+
A
B
C
D
E
F
G
2015 811/2013
A
+++
A
++
Sample Sample-1
X
X
X
X
A
+++
A
++
A
+
A
B
C
D
E
F
G
A
+++
A
++
A
+
A
B
C
D
E
F
G
+
+
+
+
2015 811/2013
A
+++
A
+++
A
++
A
Sample Sample-2
X
X
X
X
L
L
with solar thermal system
with hot-water storage tank
with temperature controller
with auxiliary heating units
The Flash Injection Circuit is an original tech-
nology. A heat exchange process at point A
(
heat interchanger
)
transforms liquid refriger-
ant into a two-phase, gas-liquid state and
then compresses the gas-liquid refrigerant
at point B (injection compressor). This circuit
secures a sufficient flow rate of refrigerant
for heating when outdoor temperatures are
very low. Thanks to improving the heat inter-
changer and introducing a new injection com-
pressor, the Flash Injection Circuit is now
more powerful.
Thanks to the unique plate heat exchanger and scale trap technology, a more efficient
performance is achieved. In conventional systems, there is a risk of calcium scale building
up on the heat-exchange plate if it is exposed to tap water directly. Therefore, it is difficult
to use plate-based heat exchangers to heat tap water. To resolve this problem, ECODAN
is equipped with a “scale trap” that catches homogeneous calcium nuclei in the tap water
before it has a chance to grow into large scales, thereby inhibiting build-up in the external
heat exchanger. ECODAN can use a plate heat exchanger to heat tap water, resulting in
much higher domestic hot water performance.
Notice: In the case of the special conditions such as very hard tap water, please consult with a specialist
before installation.
Mitsubishi Electric’s
Flash Injection Technology
The key to high heating
performance at low
outdoor temperatures
Heat interchanger
(
HIC
)
Injection compressor
A
B
Flash Injection Circuit
LEVB
LEVC
LEVA
Heat
interchanger (HIC)
A
B
Indoor
HEX
Power
receiver
Outdoor
HEX
Injection compressor
(injection port)
Flash Injection Circuit
ZUBADAN New Generation
Flash Injection Circuit
Refrigerant flow
ZUBADAN New Generation
Previous model
Integrated
capacity (kW)
Outdoor-air temperature at intake duct
W45 (according to EN 14511)
9
-7°C-15°C-20°C-28°C 0°C
10
11
12
13
14
15
Approx. 22% higher than
our previous model !
Nominal capacity can
be kept at -15ºC !
Example:
PUHZ-SHW140YHA
● Benefits ZUBADAN
New Generation
New all-in-one compact indoor unit
Indoor units
Larger capacity system
Easy to install and low maintenance
• All-in-one: Key functional components are incorporated
• Compact cylinder unit: Just 1600mm in height
• Compact hydro box: Only 600×600mm footprint
• Easy installation: Factory fitted pressure relief valve
• Easy service: Relevant parts are located at the front of
the unit for easy maintenance
• Easy transport: Handles attached on front and back
(cylinder unit)
External plate heat exchanger – more energy savings using ECODAN’s unique and
innovative technologies
High-performance for domestic hot water re-charge
*Depending on model
Hydro box (Split type)
Cylinder unit (Split type)
Water pump
Manometer
Booster heater*
Water pump
Plate heat
exchanger
Strainer
Adjustable feet
Expansion vessel*
Expansion vessel*
Booster heater*
Manometer
Domestic hot water
plate heat exchanger
Domestic
hot water pump
Tank
3-way valve
Scale trap
Plate heat
exchanger
Strainer
Outdoor units
PUHZ-SW160/200YKA
SHW230YKA2
Indoor units
EHSE-YM9EC, EHSE-MEC, ERSE-YM9EC, ERSE-MEC
Our 8–10HP ECODAN heat pumps, only available with a hydro box connection,
are suitable for large houses and small businesses where a high heating load
is necessary. Our latest generation of 8–10HP Power Inverter outdoor units
can now reach 60°C maximum flow temperature instead of 53°C previously.
The new 8–10HP hydro box is available in both heating only and reversible and
can be connected to a customised capacity domestic hot water tank.
The secret behind our external plate heat exchanger system
External P-HEX circuit
P-HEX
Scale Trap
Circulating Water
Hot Water
Fresh Water
DHW Storage Tank
Tap Water
Pump
140%
120%
100
%
80%
60%
40%
20%
0%
0 2 4 6 8 10 12 14 year
Usage condition
COP
(recharging)
<
Our test result
>
Tank temperature: 10 degree to 60 degree
Heating up time: 1 hour per 1 day
Supersaturation of CaCO
3: 50
*15 years accelerated testing
<
*
1,
*
2
>
Our new model (External heat exchanger with scale trap)
Initial performance level of previous model
(
Coil in tank
)
Save energy in domestic hot water operations
Thanks to an external plate heat exchanger, ECODAN offers much higher domestic
hot water efficiency. Compared to our previous model, domestic hot water recharge
efficiency is improved by approximately 17%*
1
, thereby reducing operating costs.
Avoid performance loss due to scale
A scale trap is incorporated after the plate heat exchanger to capture calcium scale
particles, thus maintaining the high performance of the external plate heat exchang-
er. (Just a 3% reduction during 15 years*
2
).
Lighter weight
Compared to our previous model, the cylinder unit is up to 15kg lighter*.
This is thanks to the coil incorporated in the tank which has been removed and re-
placed by a much lighter plate heat exchanger.
*Comparison between EHST20C-VM2C and EHST20C-VM2B.
Optimised stratification for better comfort
Thanks to the L-shaped inlet pipe from the plate heat exchanger, stratification is well maintained after re-charge.
You do not need to worry about running out of hot water the same as with a conventional coil in tank.
Supply water temperature can be kept high until all the hot water in the tank has been used.